The system offers options for setting minimum price and minimum quantities for labor and materials. You can also set “base costs” that will be charged every time the item is used, regardless of the final quantity.
NOTE: a “base cost” is different from a “minimum cost” because the base cost will be charged on top of the final quantity used.
-
Example of a minimum/base cost breakdown for installing 60sqft of drywall at a cost of $2/sqft
-
You have a minimum cost of $64 to cover the cost of all materials to install 1 full sheet of drywall.
-
You have a base cost of $50 to cover the setup and use of drywalling tools.
-
60 x 2= $120, which exceeds the minimum cost, so this total is used.
-
The base cost of $50 is added to the final cost of $120 for a total cost (before markup) of $170
-
-
NOTE: If the minimum cost exceeds the base cost, then no additional cost will be added if the quantity used does not force the cost above the minimum (the minimum cost is intended to capture all costs associated with the work). If you would like the base cost to be charged after the miniumum cost, you will need to use a minimum quantity instead of a minimum cost.
-
Using the example above, we will look at setting up a minimum cost for the drywall with the base cost added on top of the minimum. We will use 20sqft of drywall.
-
You set a minimum quantity of 32sqft. This ensures that you are always charging for at least 32sqft of drywall installation (effectively giving you a minimum cost of $64).
-
20sqft is less than 32, so 32sqft is used for a cost of $64.
-
The base cost of $50 is added to the $64 for a total cost of $114
-
Setting these details inside of items:
1. When creating/editing an item, click the “Advanced options” button below the total price box.
2. Every item will have an option to set a minimum price or minimum quantity.
-
The minimum price will be charged to the customer if the calculated price of all combined costs plus markup falls below the minimum.
-
The minimum quantity will be multiplied by the unit price if the dimensional quantity falls below the minimum.
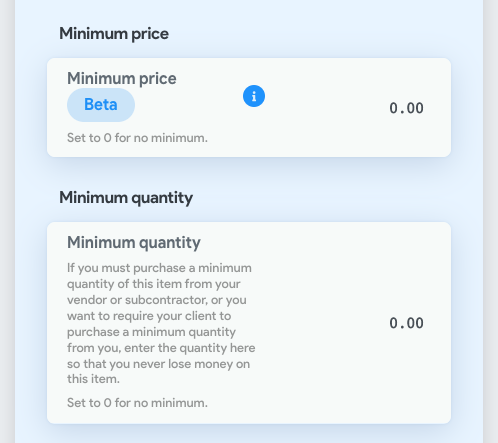
-
NOTE: If an item is multiplied on the proposal, the minimum price/quantities will still drive the final price if each unit is below the minimum. The minimums will not be multiplied for each unit.
3. If the item includes labor, the “Labor cost options” will be displayed.
-
The first group is the same labor rate details that are shown in the standard options.
-
The next option is for the “Minimum labor cost” that will be used if your dimensional cost falls below this threshold.
-
The final option is for a “Base labor cost” that will charged every time this item is used, regardless of the final quantity.
-
An example of this would be a base cost for setting up the tools required to cut the materials for the job.
-
4. If the item includes material, the “materials cost options” will display next.
-
You can set a “Minimum materials cost” that will be used if your dimensional cost falls below this threshold.
-
You can also set a “Base materials cost” that will be charged every time this item is used, regardless of the final quantity.
-
An example of this would be an “order packing” fee that your vendor charges for each material order.
-
NOTE: These values will not be multiplied if an assembly quantity is increased.
-
Minimum price example:
-
You have an item with a min price of $100 inside of an assembly.
-
You set the assembly quantity to 2 (for 2 full sets of that assembly).
-
The system will charge $50 for each unit, so the client pays the total minimum of $100
-
-
Minimum quantity example:
-
You have an item with a min qty of 200sqft inside an assembly
-
Your dimensional qty is 150sqft, so it is bumped up to the 200sqft min.
-
The assembly quantity is set to 2
-
The system uses 150sqft for each item, since the assembly total of 300sqft is over the 200 minimum.
-
-
Base cost example:
-
You have an item with a base cost of $100
-
You set the assembly quantity to 2
-
The system charges a base cost of $50 for each item in order to charge $100 total for the base cost.
-